Cold forging and pin fin heat sink capability
Cold forging and pin fin is a highly precise manufacturing process in which the workpiece is formed under high pressure and low temperature. The process ensures that no air bubbles, porosity or other impurities are trapped in the material, and thus produces products with exceptionally high quality.
Cold Forging and Pin Fin Heat Sink Advantage:
Compared with other manufacturing methods (machining, die casting, extrusion, hot forging, etc.)
● Incoming air stream from all direction
● Improved mechanical strength
● Improved surface finish
● Better control of tolerance
● Efficient use of raw materials
● Reduced energy consumption
● High production rate
● Low overall cost
In making aluminum heat sinks, cold forging can produce pins that are 50 times as tall as their diameters – an aspect ratio that is considered impossible with other methods, such as die-casting or extrusion.
Unlike stamped-fin or bonded-fin heat sinks, the pins on a forged heat sink are an integral part of its base plate – they are simply squeezed out of the base. There is no air gap or thermal interface between the pins and the base. Heat can dissipates easily from the base to the pins without additional resistance.
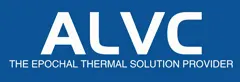
Learn more about us.
Leaving message and send us 2D/3D drawings, to analyze and solve your thermal challenges
Contact us
Sitemap
Phone:+86 135 3419 4131
E-mail : riken@alvcfactory.com
ADD :Room 802A Tower A Block 3 Tian’an Cyber Park
Huangge Road Long Gang District Shen Zhen City Guang
Dong Province China.
3rd Industrial Zone Tiantou Hengli Town Dong Guang
City Guang Gong Province China.
Cookie
Our website uses cookies and similar technologies to personalize the advertising shown to you and to help you get the best experience on our website. For more information, see our Privacy & Cookie Policy
Cookie
Our website uses cookies and similar technologies to personalize the advertising shown to you and to help you get the best experience on our website. For more information, see our Privacy & Cookie Policy
These cookies are necessary for basic functions such as payment. Standard cookies cannot be turned off and do not store any of your information.
These cookies collect information, such as how many people are using our site or which pages are popular, to help us improve the customer experience. Turning these cookies off will mean we can't collect information to improve your experience.
These cookies enable the website to provide enhanced functionality and personalization. They may be set by us or by third-party providers whose services we have added to our pages. If you do not allow these cookies, some or all of these services may not function properly.
These cookies help us understand what you are interested in so that we can show you relevant advertising on other websites. Turning these cookies off will mean we are unable to show you any personalized advertising.